Meeting July 12, 2009
Meeting - July 12, 2009
We met at Larry Sakayama's shop in Wirtz, VA.
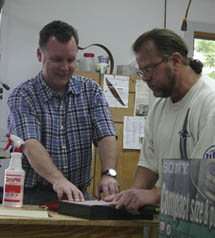
Dennis’s Sharpening Demo
Dennis showed us a technique for sharpening chisels and plane irons using sandpaper fixed to a flat surface. The basic procedure is this:
- Use wet-or-dry (aluminum oxide) sandpaper
- Temporarily fix sandpaper to a flat surface (granite stone, ¼” piece of plate glass). Dennis just wet the paper to stick it down.
- The sandpaper grit you start with will depend on the condition of your chisel.
- Lap about 1” of the end of flat side of the chisel on through successive grits (…120, 220, … 2000). Each grit should remove the scratches from the previous grit. In the end, you want a shiny, mirror like surface. Dennis uses a wisk broom to clear away the swarf.
- Then using a honing guide set to the desired angle for the cutting bevel, go through the same process above, making sure that you keep the bevel flat to the sandpaper.
- If you want, you can put a micro-bevel on the edge using whatever grade of sandpaper you finished with. You can also strop the edge.
- That’s it.
If you’re not pulling nails with your chisels, a touch up on the final grits is all you should need the next time.
For additional information do a Google search on “scary sharp system.” There’s a lot of info out there including pictures and videos.
Open Back Banjo Project
Jack Gellerstedt has agreed to lead this project. Here are some of the items we discussed. At the next meeting we can make some decisions so we can start building soon.
- Should we build one banjo, done together, or several banjos built by individuals with group consultation?
- The building process - If we do one banjo together, might we want to have an individual take it home from a meeting to do the next operations, then pass it on at the next meeting to someone else? On the Steve Parks Signature Guitar, we did some of this.
- Where should we do most of the work? My (Jack's) place is ok, but pretty distant for most of you, and my tools are limited. There are, however, a couple of operations that would be best done here (heel cuts, mainly), but the rest could be done anywhere.
- Banjo style (tone ring type, decoration, etc.) - we can decide this at the next meeting. Jack has some ideas and will bring them to the meeting.
- We should build a "quality" instrument, not necessarily fancy, but high grade regarding function and craftsmanship. We want it to look good, play well and sound great.
- Project Cost -Parts for such an instrument would probably run about $500, which sounds high,
but a banjo has more manufactured parts than some of the other instruments.
- Jack will make a detailed parts list with prices before the meeting.
- Options for funding: Ask for donations, group gig, individual contributions...
- What happens to the finsished banjo? Some options:
- Donate it to a charitable cause
- Sell it and use the funds for the next project
- Sell it and donate the funds
- If individuals wish to make their own instrument they can do so for somewhat less cost, mainly by choosing a less expensive tone ring, which will still sound very good. And, regardng playability, this depends entirely on the quality of their own workmanship.
- Making a metal spun rim - We discussed the option of making a metal spun rim but this involves a lot of experimentation in an arena that would not have much carry-over value to other instrument projects.